How to Select the Right Pelletizer Machine with Lower Cost?
- Share
- publisher
- Mira
- Issue Time
- Aug 20,2019
Summary
We often classify pelletizing processes into two categories, differentiated by the state of the plastic material at the time it's cut:
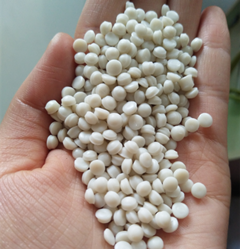
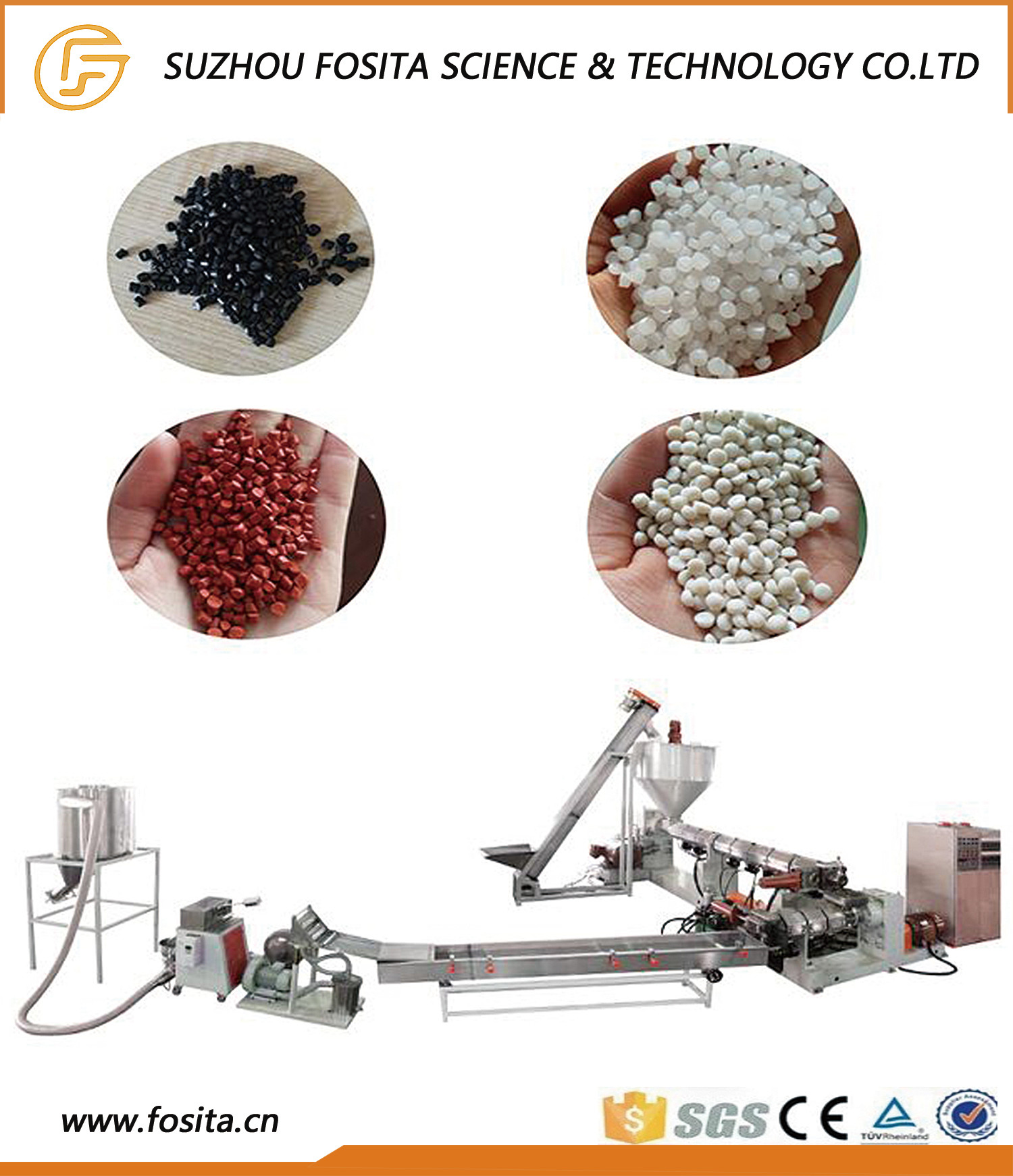
We often classify pelletizing processes into two categories, differentiated by the state of the plastic material at the time it's cut:
•Melt pelletizing (hot cutting): Melt coming from a die that is almost immediately cut into pellets that are conveyed and cooled by gas or liquid;
•Strand pelletizing (cold cutting): Melt coming from a die head is converted into strands that are cut into pellets after cooling and solidification.
Underwater strand pelletizing is a sophisticated automatic process. But this method of production is used primarily in some virgin polymer production, such as for polyesters, nylons, and styrenic polymers, and has no common application in today’s compounding.
Air-cooled die-face pelletizing is a process applicable only for non-sticky products, especially PVC. But this material is more commonly compounded in batch mixers with heating and cooling and discharged as dry-blends. Only negligible amounts of PVC compounds are transformed into pellets.
Water-ring pelletizing is also an automatic operation. But it is also suitable only for less sticky materials and finds its main application in polyolefin recycling and in some minor applications in compounding.
When the preferred pellet shape is more spherical than cylindrical, the best alternative is an underwater hot-face cutter. This system is applicable to all materials with thermoplastic behavior. In operation, the polymer melt is divided into a ring of strands that flow through an annular die into a cutting chamber flooded with process water. A rotating cutting head in the water stream cuts the polymer strands into pellets, which are immediately conveyed out of the cutting chamber. The pellets are transported as a slurry to the centrifugal dryer, where they are separated from water by the impact of rotating paddles. The dry pellets are discharged and delivered for subsequent processing. The water is filtered, tempered, and recirculated back to the process.