PET Bottle Flake Recycling and Washing Machine Manufacturer Fosita Company
- Model
- FST-300/500/1000
Item specifics
- Application:
- PET recycling and washing
- Voltage
- 380V 50Hz
- Power
- 80-250KW
- Weight
- 5-10T
- Certification
- CE
- Warranty
- 1 year
- Plastic type:
- pet bottle,water bottle and flakes
- After-sales service
- Field maintenance and repair service
- Capacity
- 300-2000kg/h
Review
- B***a
- 2019/8/9 09:40
It's my first time to do business in China and I chose Fosita because of professional guidance and good after-sales service.I think this line is the best proposal for PET recycling.
Description
Product Description
PET Bottle Waste Plastic Recycling Machine
Fosita PET bottle waste plastic recycling machine is mainly used for crushing, washing, palletizing of PET bottles to realize auto separation for caps and labels: belt conveyer, crusher, steam washer, scrubbing washing unit, rinsing and precipitation washing unit, centrifugal dewatering unit, hot air flow drying unit, and electric control cabinet.
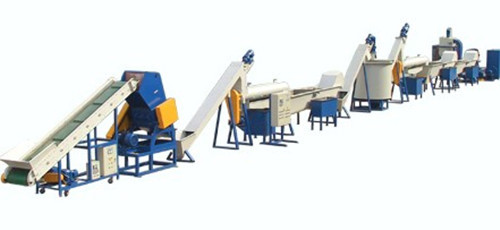
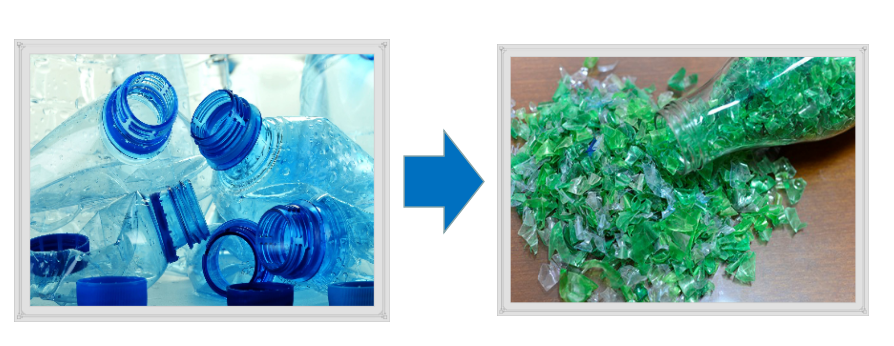
Advantages
1.Through crushing, washing and dry process, the waste bottle or sheet will become to be bottle flakes. The flakes are widely used in plastic industry, like sheet, and profile production.
2.The clean flakes can be used to produce the polyester staple fiber, PET strap band, granules, PET transparent film and sheets, etc. The top class flakes can be used to blow bottles again.
3. Plastic recycling machine can be designed on the basis of how dirty the flakes are, and make sure of the quality of the final products are very clean.
4. Plastic recycling machine output we can supply is from 300kg/h to 2000kg/h.

Work Processing
PET Bottle Waste Plastic Recycling Machine
Belt conveyer → Rolling separator →Manual pick table → Metal separator → Belt conveyer → Crusher → Label Separator → Hot washer 1 → Friction washing machine → Hot washer 2 → High-speed friction washing machine → Rinsing tank → Spray washing→ Dewatering machine → Blower dryness system → Storage hopper → Finished product packing

Features:
Capacity: 300—2000kg per hour
Moisture of PET Flakes: Less Than 2%,Cap &Label separate with the PET bottle flakes automatically
Bottle Types: PET Bottle, Plastic Bucket, Water Bottle, Coke Bottle,
Application: PET Strap, PET Yarn Fiber
CE Standard: Provide Turn Key Solution.
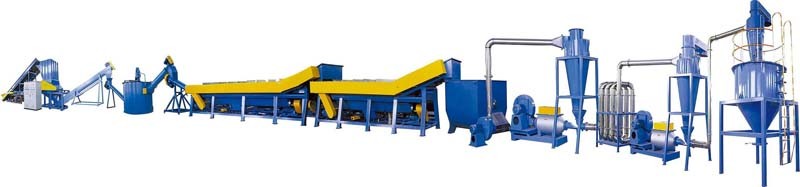
Technical Parameter
Pipe Line Model
|
Total Power(kw)
|
Output(kg/h)
|
LIne Length(m)
|
FST-300
|
90-120
|
200-300
|
25
|
FST-500
|
130-145
|
500-600
|
30
|
FST-1000
|
150-190
|
800-1000
|
40
|
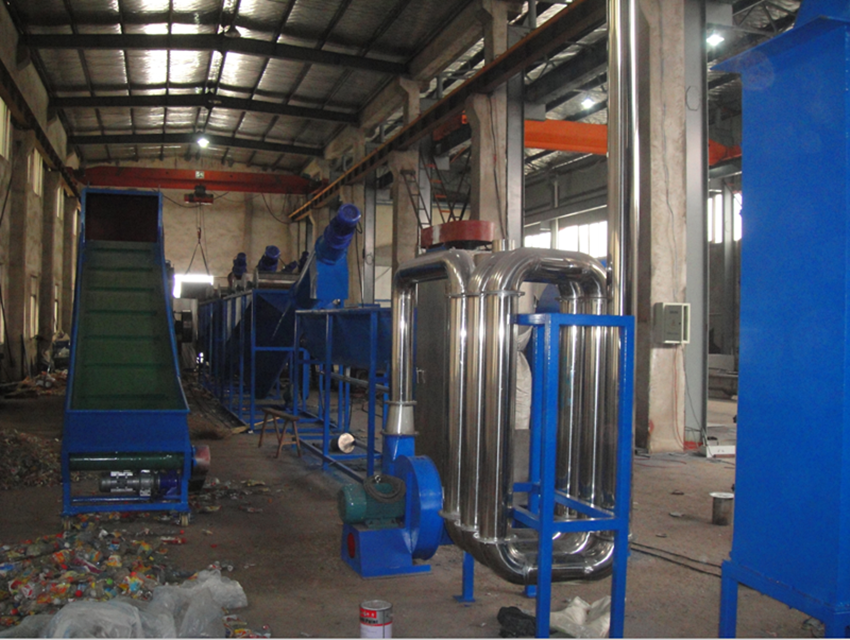
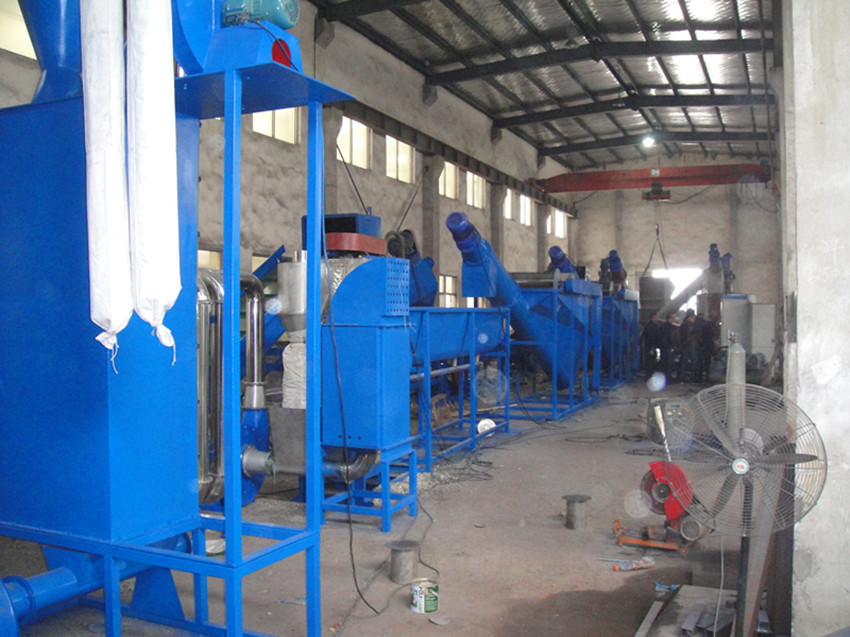
Working Video Please Click:www.youtube.com
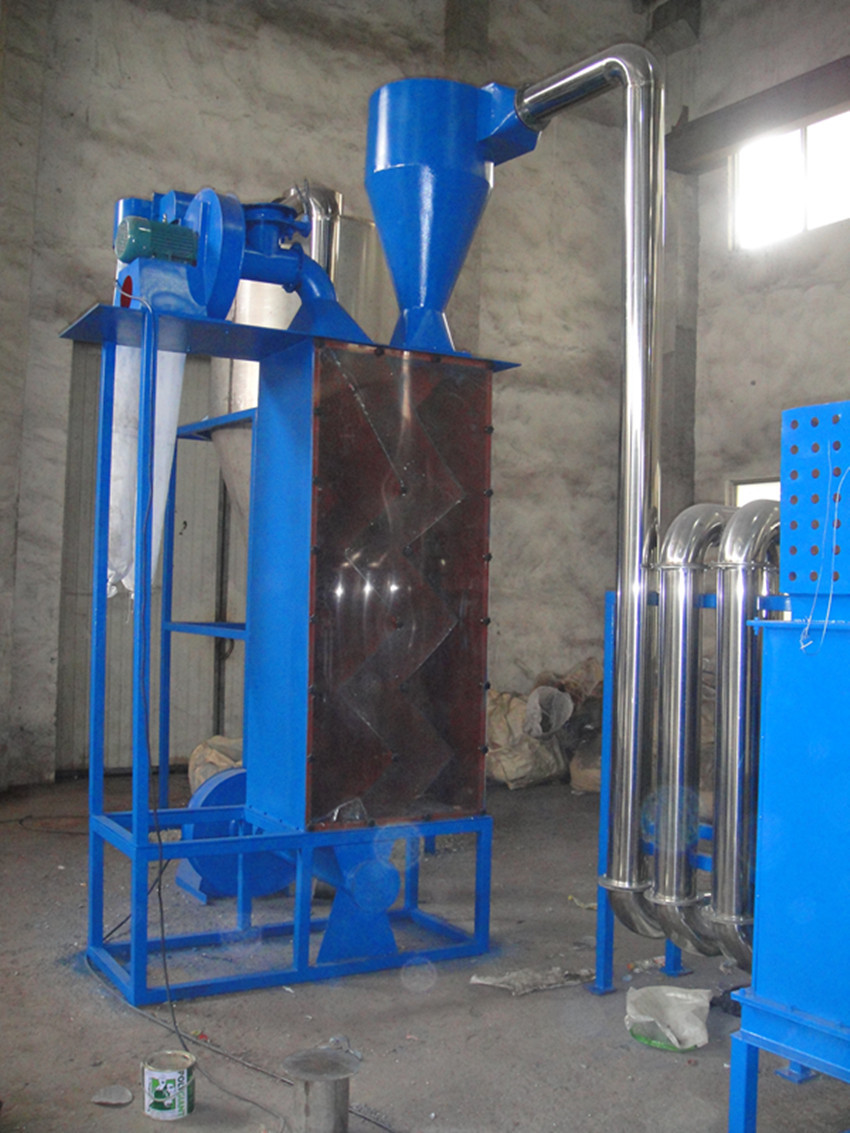
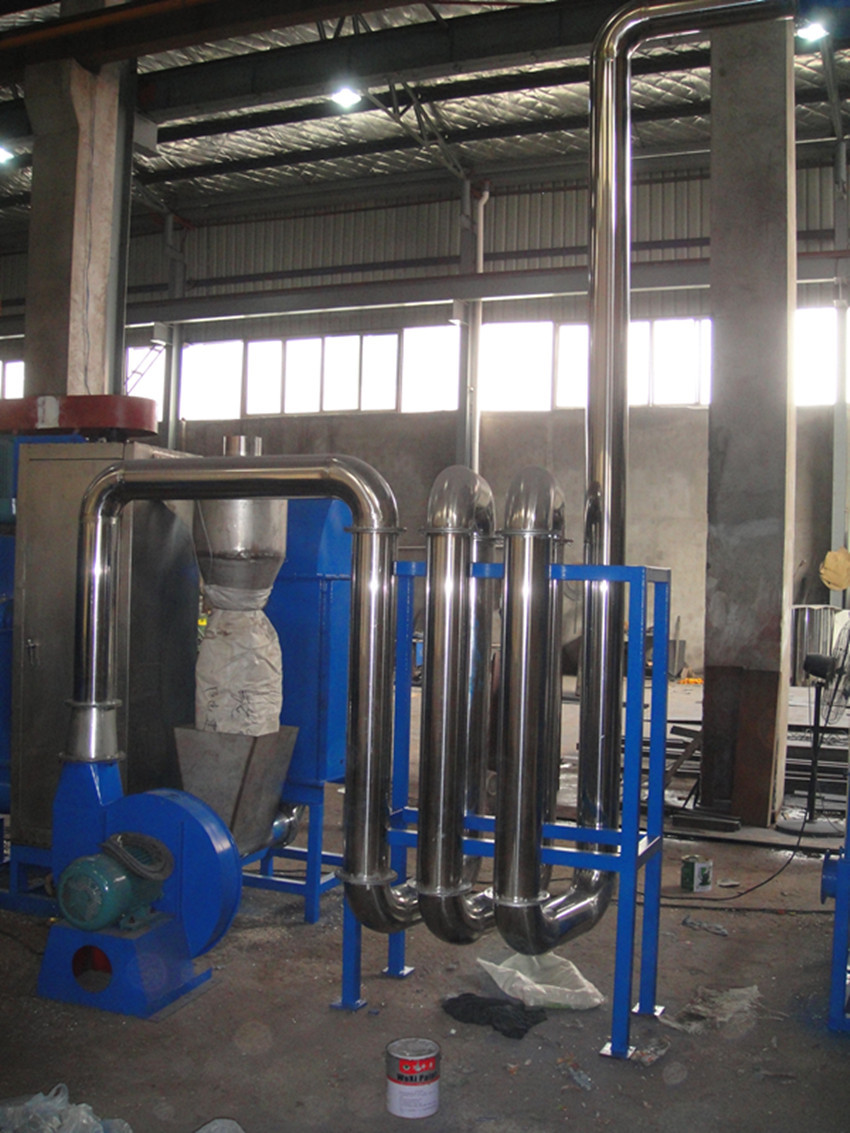
Configuration table
No.
|
Machine List
|
Description
|
|
1
|
Prewasher
|
Remove the solid impurity which are water insoluble, such as hand stone, sand, etc. It can also wash bottles' surface.
|
|
2
|
Bale Breaker
|
It is used in large capacity recycling line, and bottles are compressed in bale.
|
|
3
|
Belt Conveyer
|
Including the metal detector.
|
|
4 | Label Remover | Label removing efficiency, more than 98% | |
5 | Manual Select Platform | Made according to workers' height, supply a suitable plate for selecting the left labels or some other impurity. | |
6 | Belt Conveyer | Conveying the bottles into crusher. | |
7 | Crusher | With water, the materials of the blade adopt SKD-II or 9CrSi. It has a function of prewashing too. | |
8 | Screw Feeder | Conveying the flakes into friction washer. | |
9 | Friction Washer | Scrubbing material in high-speed with water. | |
10 | Screw Floating Washer | Remove few remand paper, sand, label from material based on different density. | |
11 | Screw Feeder | Conveying the flakes into hot washer. | |
12 | Hot Washer | High temperature stirring washing with caustic soda. Water can be heated by steam or electric. | |
13 | Screw Feeder | Same as Item 8. | |
14 | Friction Washer | Same as Item 9. | |
15 | Screw Floating Washer | Same as Item 10. | |
16 | Dewatering Machine | High speed centrifuge drying. | |
17 | Drying System | Electric heating wind drying. | |
18 | Label Wind Separator | The last left impurity will be separated from flakes by the blower fan. | |
19 | Silo | Store the final material. | |
20 | Electrical Control Panel | Adopts Siemens and DELIXI as main component. |
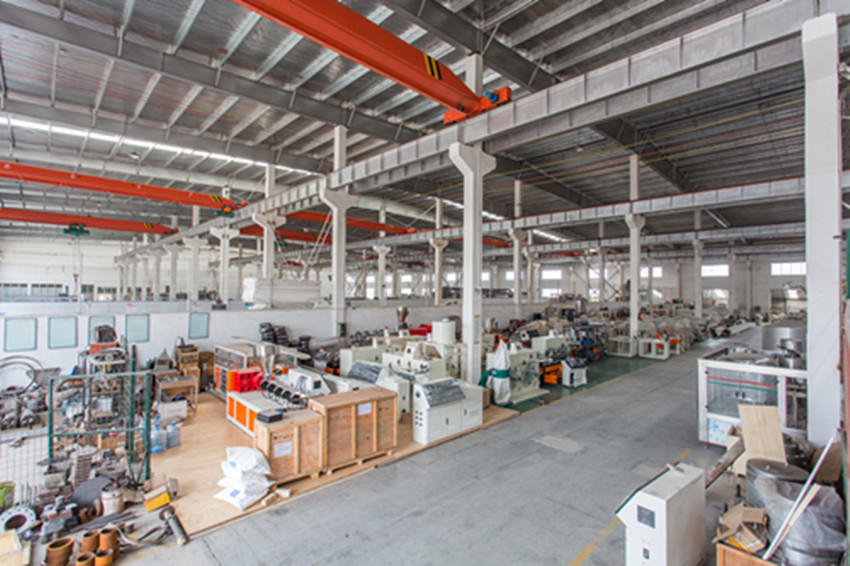
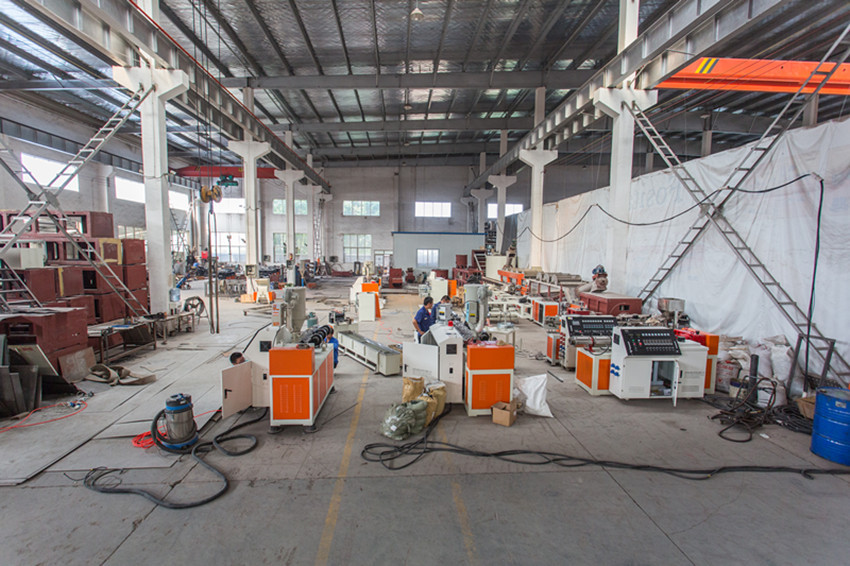